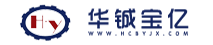
含油污泥是指原油或成品油混入泥土或其他土壤介質(zhì),油分不能直接回收而可能造成環(huán)境污染的多種形態(tài)的混合物。含油污泥一般是油包水、水包油型浮狀液和懸浮固體組一起成的穩(wěn)定體系,其脫水效果差,處理難度大,并且污泥的成分和物理性質(zhì)會受污水水質(zhì)、處理工藝、投加藥劑等因素的影響,差異性會非常顯著。而且含油污泥含有重金屬、多環(huán)芳烴等有害物質(zhì),而且有時含有一定的放射性,必須進行無害化處理。以新疆油田為例,每年產(chǎn)生的石油泥渣約為2×104t,已堆存的油泥總量達20×104t,對石油泥渣的無害化處理工作已迫在眉睫。
1 油田含油污泥的來源
(1)原油開采過程產(chǎn)生的含油污泥。油田聯(lián)合站儲油罐產(chǎn)生的大罐沉降污泥、鉆井及井下作業(yè)產(chǎn)生的含油污泥、污水凈化處理中產(chǎn)生的含油污泥、設(shè)備及管道腐蝕產(chǎn)物和垢物、細菌(尸體)等,構(gòu)成了油田含油污泥。
(2)油田集輸過程產(chǎn)生含油污泥。這類污泥包括油田轉(zhuǎn)接站罐底泥、隔油池底泥、天然氣凈化和輕烴加工裝置清除出來的油泥、管線穿孔產(chǎn)生的落地原油等。
2 含油污泥的性質(zhì)及危害
2.1 含油污泥的性質(zhì)
含油污泥一般可以分為落地原油和罐底油泥。罐底油泥含油量要顯著高于落地油泥,且二者中膠質(zhì)和瀝青質(zhì)的含量基本相等,處理時需要降低油與固體顆粒之間的吸附性能,以此提高油泥的分離效果。從掃描電鏡及殘渣形態(tài)分析可看出,落地油泥以沙土為主,比重較大,經(jīng)過熱水分散作用容易達到三相分離的目的。罐底油泥無機元素含量高,尤其是鐵元素,通過堿水洗滌可以除去油相中的無機雜質(zhì)。熱洗可以改善油泥的粘稠度以及流動性,化學(xué)藥劑可以對油泥進行絮凝破乳,達到較好的三相分離的目的,因此通過化學(xué)藥劑和機械的同作用能夠?qū)崿F(xiàn)油泥的分離。
2.2 含油污泥的危害
含油污泥中除含有大量殘留油類外,還含有苯系物、蒽、酚類、芘等有毒物質(zhì),大量的寄生蟲、病原菌以及Cr(27~80mg/kg)、Cu(32~120mg/kg)、Pb(0.001~0.120mg/kg)等重金屬,以及多氯聯(lián)苯、二英、放射性元素等有毒有害物質(zhì)。含油污泥體積龐大,若不進行處理而直接排放,會占用大量耕地,而且對周圍的水體、土壤、空氣都會造成嚴重污染。這些污染物還能通過食物鏈在動植物和人體內(nèi)逐級富集,造成嚴重的危害。
3 含油污泥處理工藝
3.1 調(diào)質(zhì)-脫水處理工藝
污水處理過程產(chǎn)生的含油污泥其含水率高,一般可以達到百分之九十以上,體積龐大,運輸非常困難。調(diào)質(zhì)-脫水是預(yù)處理的主要工藝方法,也可以脫水后直接進行固化或者填埋處理。調(diào)質(zhì)是通過化學(xué)或物理手段來調(diào)整粒子群的物理性狀及排列狀態(tài),使之適合不同的脫水操作處理,以此提高機械脫水的性能。確定污泥的調(diào)質(zhì)-脫水處理工藝流程最重要的是選定合適的在調(diào)質(zhì)用的有機無機調(diào)節(jié)劑、有機絮凝劑種類及用量、選擇脫水機械的類型及運行參數(shù)。研究證明,有機高分子絮凝劑能夠破壞膠體的穩(wěn)定性,從而增強含油污泥的脫水性能,使得含油污泥的含水率下降,最多可下降至90%以下。研究和開發(fā)絮凝效果好,適應(yīng)范圍廣,無毒無害的生物絮凝劑,越來越引起各國科研工作者的重視。
周文武曾報道了通過濃縮-淘洗除鹽-浮選除油-壓濾脫水為主體的油田含油污泥處理工藝流程。此法是先進行污泥濃縮,污泥在加藥濃縮4h左右后,含水率可由原來的99.5%降至85%左右。然后,采用逆流淘洗法,即使污泥流向與淘洗水流向方向相反,淘洗水采用清水,污泥和淘洗水的體積比在1:2~1:6之間,一般為1:3。經(jīng)過三級逆流淘洗,可使污泥的含鹽量降到30mgL以下。經(jīng)過除鹽之后的污泥進入浮選除油系統(tǒng),通過加入合適的浮選藥劑,經(jīng)過充分的攪拌而達到浮選除油的目的。調(diào)節(jié)好的污泥最后送入壓濾機進行壓濾。當充氣量為0.12~0.15m3/h;刮泡速度為30次/min;攪拌強度達到1200r/min;清水:污泥=1:1;抑制劑150mg/L,調(diào)整劑150mg/L,捕收劑130mg/L時,浮選凈化污泥的濃縮沉降性能很好,經(jīng)8min沉淀,其含水率可降到85%以下。使用CPF型帶式壓濾機進行壓濾,出料泥餅的含水降至30.78%,含油0.37%,含鹽0.5%,含泥68.35%,其體積僅為處理前的1/3~1/4,減少了污染,大大方便了運輸和堆放。調(diào)質(zhì)處理雖然是一種早期的簡單的處理方法,但是取得了很好的效果。
3.2 高溫處理工藝
高溫處理是在高溫,無氧的條件下對含油污泥進行的處理。含油污泥的高溫處理主要包括高溫熱解和焦化處理。國外對污泥熱解技術(shù)的研究較早,但國內(nèi)起步較晚,目前進展較快,一般處于室內(nèi)研究階段。含油污泥的熱解可以分為三個階段:水分揮發(fā)階段、揮發(fā)分揮發(fā)階段以及固定碳燃階段,當溫度較低時,含油污泥進行的是水分和揮發(fā)分揮發(fā);當溫度超過固定碳燃盡所需溫度時,碳元素揮發(fā),碳骨架結(jié)構(gòu)坍塌,礦物質(zhì)主要是碳酸鈣發(fā)生分解。裂解過程中可投加催化劑,以提高輕質(zhì)油收率,降低熱解溫度。
李金林、莊貴濤等報道通過采用美國專利含油污泥超熱蒸汽處理技術(shù),形成了一套處理含油污泥的新工藝,即污泥-重力濃縮罐-離心脫水機-螺旋輸送機-超熱蒸汽噴射干化裝置-外運摻煤進燃煤鍋爐焚燒。含油污泥首先進入污泥濃縮罐,通過重力沉降降低含水率,隨后污泥進入離心機離心脫水,最后進入超熱蒸汽噴射干化裝置,氣體組分冷凝收集,固體灰分和燃煤混合供鍋爐燃燒。當污泥的進樣含水率在97%~99%時,污泥濃縮罐設(shè)計泥固體負荷為50kg/(m2/d),污泥濃縮罐出口的污泥含水率可降到96%~98%,污泥的體積減少了一半。在污泥進離心機之前投加絮凝劑,有機絮凝劑確定為CPA,投加量是100~150mg/L。處理后污泥經(jīng)污泥提升泵進入離心機,在污泥提升泵吸泥口處設(shè)置粉碎切割機。離心機設(shè)計的處理量為20m3/h,出離心機的泥餅的含水率可以降至75%~80%。在螺旋送料器的作用下,進入超熱蒸汽噴射干化室,600℃超高溫蒸汽經(jīng)過特制的噴嘴高速噴出,粉碎污泥。油和水一起被蒸發(fā)出來,粉碎的細小顆粒連同蒸汽進入氣旋室,在旋流的作用下實現(xiàn)蒸汽和固體顆粒的分離,剩余固體殘渣含水率<20%,含油率<0.1%,且均為不易揮發(fā)的重組分。最后呈粉末狀直接進入回收槽,可以直接移入熱電廠煤粉中一起進行灼燒處理。
焦化法處理含油污泥是對重質(zhì)油的深度熱處理,反應(yīng)過程是油泥中烴類物質(zhì)的熱轉(zhuǎn)化過程。很多煉廠20世紀90年代就開始采用Mobil油泥焦化工藝來處理隔油池污泥。趙東風(fēng)等提出處理流程如下:原料經(jīng)預(yù)處理后除去較大的機械雜質(zhì),與一次性催化劑摻和后利用傳輸設(shè)備一并送人預(yù)熱好的焦化反應(yīng)釜,閉釜加熱進行反應(yīng)。將反應(yīng)溫度控制在490℃,反應(yīng)時間控制在60min。焦化反應(yīng)氣經(jīng)過伴熱管線進入三相分離器,由循環(huán)水控制三相分離器降溫,三相分離器上部氣相組分送入燃燒系統(tǒng)回收利用;底部含油污水送入污水處理系統(tǒng),回收油進入儲罐儲存,最終取得良好的效果。焦化法處理含油污泥對污泥的含油量要求不高,但整個工藝過程復(fù)雜,投資較大。
3.3 萃取處理工藝
萃取法處理含油污泥利用了石油類物質(zhì)在不同兩種互不混溶的溶劑中的溶解度不同的性質(zhì),使石油類物質(zhì)從水相轉(zhuǎn)移到有機相中,然后利用石油烴與有機溶劑沸點的不同,通過蒸餾的方法,使石油類物質(zhì)與溶劑分開,而溶劑又重新回用于處理系統(tǒng)中,提取出的石油烴得以回收再利用。但是,萃取劑在回收循環(huán)的過程中會出現(xiàn)部分遺失,使得處理成本偏高。因此開發(fā)出性價比高的萃取劑就成了此項技術(shù)發(fā)展的關(guān)鍵。并且萃取后泥渣需進行進一步處置,萃取工藝就必須與其他處理處理方法結(jié)合使用。
李慧敏,張燕萍等報道了“含油污泥熱洗+助溶劑萃取技術(shù)”,先使含油污泥進入油泥混合機,將塊狀泥塊弄碎,與洗滌劑攪拌混合,同時進行粗料與細料的分離,粗料(5mm以上砂石,雜物)經(jīng)過粗料洗滌機洗滌,達標外運,細料打入洗滌槽洗滌后進行三相分離。分離出來的油分經(jīng)過油分離槽進行油水分離后進入儲油槽;分離出來的洗滌液則泵至洗滌液循環(huán)槽循環(huán)使用;污泥則泵至離心機進行離心脫水,經(jīng)檢測污泥達標則可外運,若不達標則進入前端洗滌槽內(nèi)循環(huán),直至達標。含油量為8%-30%的污泥,經(jīng)過該工藝處理,含油污泥中的礦物油含量可降至0.3%以下,達到GB4284-84《農(nóng)用污泥中污染物控制指標》中的控制要求。
3.4 生物處理工藝
含油污泥生物處理技術(shù)是利用微生物對油泥中的有機物進行消耗降解,在微生物的生長繁殖的過程中,會將石油類物質(zhì)消耗降解,最終轉(zhuǎn)化為C2O和H2O等無機物,其優(yōu)點:能耗低,處理成本低,避免了污染物的多次轉(zhuǎn)移,綠色環(huán)保;缺點:石油降解用到的微生物的篩選、培養(yǎng)以及工藝設(shè)計不夠成熟;不能用于處理含油率較高的污泥,且處理周期長。宋紹富等通過對延長油田含油污泥進行微生物堆制處理,經(jīng)過35天,YC-1菌與YC-13菌對含油污泥的出油率分別達到43.41%和54.02%。王新新等采用堆肥方法處理含油污泥,評價堆肥處理對含油污泥中石油烴的去除效果,并采用Biolog方法和構(gòu)建16SrRNA基因克隆文庫的方法對處理過程中微生物碳源利用特征和微生物群落結(jié)構(gòu)進行了研究。含油污泥經(jīng)過90d的堆肥處理后,石油烴降解率達到53.3%±9.5%,明顯高于對照處理。堆肥處理可顯著促進石油烴的降解,是一種處理含油污泥的有效方法。
3.5 調(diào)剖處理工藝
調(diào)剖技術(shù)處理含油污泥是利用含油污泥與地層的良好的伍性,利用化學(xué)方法,加入乳化劑及懸浮劑等,將含油污泥的泥組分、油組分和添加劑等制成含油污泥調(diào)剖劑回注地底,能有效封堵高滲透層注水孔道。從而達到調(diào)整注水剖面和提高采收率的目的。
調(diào)剖處理工藝利用傳送裝置將含油污泥傳送至配制罐攪拌,將懸浮劑、稀釋劑和乳化劑加入到罐中,攪拌均勻。然后檢測泥漿的粘度、密度,達設(shè)計要求后,用泥漿泵將含油污泥調(diào)堵劑注入井內(nèi)。劉玉介紹了大慶長垣油田含油污泥深度調(diào)堵技術(shù),全井調(diào)堵液設(shè)計用量為4000m3,調(diào)堵半徑40m,停注壓力1115MPa,設(shè)計調(diào)堵劑分三個段塞注入:第一階段,污泥調(diào)堵劑的密度為1110~1115g/cm3,馬氏漏斗粘度低于60s,注入量為2800m3;第二階段,污泥調(diào)堵劑的密度為1115~1125g/cm3,馬氏漏斗粘度70s左右,注入量為1000m3;第三階段,污泥調(diào)堵劑的密度為1130g/cm3以上,馬氏漏斗粘度70~90s,注入量為200m3?,F(xiàn)場調(diào)堵試驗在2005年8月進行,共計注入油泥漿5200m3,平均日注量為190m3。試驗結(jié)果23口試驗井平均注入壓力從試驗前6164MPa上升到7174MPa,連通油井單井增油218t,含水下降117%,污泥調(diào)堵增油降水效果明顯,注人層剖面得到明顯改善。
4 結(jié)束語
含油污泥的處理工藝很多,每種方法都有自身的優(yōu)缺點以及使用范圍。我國多數(shù)油田采用的主要方法是將含油污泥調(diào)質(zhì)脫水處理后制成泥餅等簡單的處理措施,但這種方法再很大程度上會引起環(huán)境污染問題。高溫處理可以實現(xiàn)資源的回收利用,但投資比較大,工藝還不是足夠成熟,由于在處理過程中需要添加昂貴的化學(xué)藥劑以及相匹配的處理設(shè)施,處理過程復(fù)雜、成本較高,而且還會引起廢水、廢渣等二次污染問題,需要進一步處理利用。萃取法可以提取出油分,但萃取劑的損失及其所帶來的經(jīng)濟問題,是制約萃取工藝發(fā)展的一個重要因素。生物及調(diào)剖處理雖然處理效果好,完全沒有污染,但處理量有限。隨著各項處理技術(shù)的日臻完善,新型廉價萃取劑以及以石油烴類為唯一碳源、高耐受性的工程菌的研發(fā)是今后研究的重點?;瘜W(xué)一生物、物理一化學(xué)等調(diào)理措施的聯(lián)合將是今后的主要方向研究,同時由于含油污泥的成分復(fù)雜,及時分級、分階段的處理工藝也將是今后含油污泥的無害化處理和資源化發(fā)展方向。