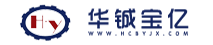
遼陽石化公司煉油和化工幾大主體生產(chǎn)裝置經(jīng)擴能改造投產(chǎn)運行后下排污染質(zhì)總量持續(xù)上升,污水處理裝置運行時污泥產(chǎn)量相應(yīng)增大。污水處理廠初沉淤泥、含油污泥、剩余活性污泥(以下簡稱“三泥”),是污水生化處理裝置的前置預(yù)處理單元產(chǎn)生。污泥中含有苯系物、酚類、硫化物、氰化物等具有惡臭味和毒性的物質(zhì),是國家明文規(guī)定的危險廢物,比較難于生物降解。含油污泥已被列入《國家危險廢物目錄》中的含油廢物類,《國家清潔生產(chǎn)促進法》要求必須對含油污泥進行無害化處理。含油污泥的處理與應(yīng)用是國內(nèi)外石油生產(chǎn)領(lǐng)域環(huán)境保護的重要內(nèi)容,是較難解決而又急需解決的問題之一,也是制約石油化工環(huán)境質(zhì)量持續(xù)提高和經(jīng)濟可持續(xù)發(fā)展的一大難題。多年生產(chǎn)實踐經(jīng)驗告訴我們:對于“三泥”的收集和有效處理,其運行效率將極大地影響到污水微生物生化處理效果和水質(zhì)排放達標,對改善周圍生活環(huán)境和保護地下水資源意義重大。
1 生產(chǎn)概況及現(xiàn)狀分析
該公司煉油污水處理裝置主要負責(zé)處理煉油裝置高含油污水、部分化工裝置低含油污水及部分生活區(qū)污水。配套污泥脫水系統(tǒng)主體設(shè)備為德國產(chǎn)福樂偉離心脫水機,其設(shè)計處理能力為35m3/h,實際生產(chǎn)為間歇運行。污泥脫水系統(tǒng)每天處理約100m3含水率99%濕污泥及浮渣底泥,產(chǎn)生約10m3含水率90%左右干污泥裝車外運至后續(xù)處理單元,脫水后濾液經(jīng)檢測懸浮固體含量(SS)為400mg/L左右,直接回流至裝置入口。這些生產(chǎn)數(shù)據(jù)充分說明了污泥處理系統(tǒng)遠沒有達到連續(xù)運行負荷和較高的運行效率。
一般情況,收集和濃縮后的污泥含固率為1%~2.5%,經(jīng)過化學(xué)藥劑調(diào)質(zhì)后泵送至離心機脫水處理后干污泥含固率達10%以上,分離出來的濾液含固率不高于0.5%。大部分污水處理廠污泥經(jīng)脫水后濾液直接回流至污水裝置入口,如泵前池或者初沉池入口進行再次沉淀分離。這樣,經(jīng)常出現(xiàn)集水池淤積堵塞提升泵吸入口管道和底閥的情況,也常常造成初沉池排泥困難。主要的是實際生產(chǎn)過程中,待脫水污泥是來源于初沉池的池底淤泥、氣浮池底泥及浮渣、中間沉淀池脫落生物膜等混合介質(zhì),經(jīng)過脫水分離出來的濾液成分比較復(fù)雜,如果含固率(SS)含量較高的情況下,不加以處理直接流入某一預(yù)處理單元易造成不利于后續(xù)工藝穩(wěn)定運行的問題。因此,污泥壓濾系統(tǒng)優(yōu)化運行無疑是污水生化裝置平穩(wěn)運行、達標排放的重要環(huán)節(jié)。
2 技術(shù)改造及工藝完善
為了使污泥處理單元達到更高的運行效率,濾液再處理不失為有效可行的技術(shù)方向。經(jīng)過研究論證,通過對濾液增加后續(xù)處理設(shè)備,一方面不僅使濾水SS含量降低而極大提高脫水系統(tǒng)對污泥處理處置的綜合回收率,另一方面使離心機的操作條件更加寬松和達到更高的脫水率,污泥減容效果十分明顯。結(jié)合以往運行經(jīng)驗和經(jīng)過研究論證,我們認為——污泥脫水含水率低于80%,濾液處理SS達30mg/L以下是較經(jīng)濟合理的運行方式和生產(chǎn)目標。氣浮技術(shù)作為一種高效、快速的固-液分離技術(shù),已廣泛應(yīng)用于石油化工廢水的處理,去除廢水中油脂和懸浮物。
目前石化行業(yè)普遍采用的氣浮技術(shù)是加壓溶氣氣浮工藝和渦凹氣浮工藝。渦凹氣浮工藝采用水力切割法制造微氣泡,產(chǎn)生氣泡較大,一般在100um以上,生成浮渣穩(wěn)定性差,出水SS偏高,在實際運行過程中經(jīng)常發(fā)現(xiàn)中空管堵塞和諸多機械故障問題不利于長周期穩(wěn)定運行。經(jīng)過考察和技術(shù)交流,我們發(fā)現(xiàn)加壓溶氣氣浮產(chǎn)生氣泡一般在60~100um,對乳化油和較高SS濃度去除效果明顯,具有能耗低、易于維護和利于長周期運行等特點,已成為含油廢水處理的優(yōu)選工藝。經(jīng)過改造升級后,增設(shè)了配套溶氣氣浮裝置,處理能力為50m3/h。同時,增設(shè)了相應(yīng)污泥調(diào)節(jié)池和工藝聯(lián)絡(luò)管道,經(jīng)調(diào)試后確實解決了濾水懸浮固體含量較高的問題,提高污泥脫水效率,同時取得了十分穩(wěn)定的處理效果。
3 優(yōu)化控制參數(shù)及運行數(shù)據(jù)
3.1 離心脫水機
假定離心機的分離污泥密度為p1,污泥顆粒直徑為d,污泥的黏度為u,水相密度為p2。污泥在離心速度為ε=w2×r的離心脫水機中的離心沉降速度v滿足stock公式,即:
V=w2×r(p1-p2)d2/18u
式中ε和重力加速度g的比值即為離心因數(shù)α,經(jīng)過變換可得:
V=α(p1-1)d2/1.83u
由上式可知,污泥懸浮顆粒在離心機內(nèi)的沉降速度v與其粒徑d的平方、粒徑和水相的密度差(p1-1)、離心機的離心因數(shù)α成正比,而和污泥混合液的黏度u成反比。因此,污泥顆粒與水相之間的密度差是含油污泥離心分離的前提條件,為了提高和保證離心分離效率,可增大污泥顆粒粒徑和密度,減少自身黏度,適當提高離心速度。調(diào)試過程中要特別注意的是脫水污泥含水率和濾液中SS水平平衡點。在相同運行負荷下,若要取得脫水污泥較低的含水率勢必造成濾液較高的懸浮固體(SS)含量,增加了后續(xù)工藝處理負荷和降低了離心脫水機的處理效率;同樣,如果達到了較好的濾液排放水平必然也會增加污泥含水率,大大增加了排放容積和處理成本。
采用PAM藥劑用量與運行參數(shù)優(yōu)化實驗,將主機轉(zhuǎn)速、差轉(zhuǎn)速、污泥量、藥劑量4個因素,每個因素采用3個穩(wěn)定運行檔差(位級)進行正交實驗,得出主要的并已經(jīng)過穩(wěn)定運行驗證的參數(shù):主機轉(zhuǎn)速為2600r/min、差轉(zhuǎn)速為3~5轉(zhuǎn)、藥液配制濃度0.3%、污泥流量32m3/h、藥劑流量800L/h。脫水機在穩(wěn)定運行同時取得了較好的處理效果,確保了污泥減容,解決了以往剩余污泥脫水后容積大的問題。生產(chǎn)中脫水后外運“干泥”含水率低于80%,污泥外運體積減少了約48%,經(jīng)過初步統(tǒng)計泥餅含水率平均值為78.8%。
3.2 溶氣氣浮裝置
溶氣氣浮裝置在進水SS低于800mg/L、油含量低于500mg/L的情況下出水水質(zhì)穩(wěn)定。在調(diào)試過程中,濾液處理量約30m3/h,我們將溶氣壓力控制為0.40MPa達到氣泡均勻,經(jīng)過反復(fù)對比控制,分離的濾水回流比為20%左右,浮渣達到較好的上浮效果。同時,反應(yīng)器設(shè)置擴徑及速率控制在約0.80m/s;0.3%PAM藥液配制濃度下投加量為300L/h;20%濃度PAC投加量為500L/h。氣浮出水經(jīng)過分析取樣化驗,懸浮物含量低于30mg/L,含油量低于2mg/L。
濾液經(jīng)過穩(wěn)定運行的氣浮裝置處理降低了出水懸浮物濃度,生產(chǎn)現(xiàn)場絮凝藥劑PAM優(yōu)化篩選及合理加藥濃度確保污泥絮凝性能和泥水分離效果,提高該系統(tǒng)處理效率和回收率,使污泥脫水系統(tǒng)下排濾液懸浮物SS低于30mg/L,平均值為27mg/L,去除率達95%以上。
4 效益分析
節(jié)約污泥運輸費用:脫水污泥含水率達到78.8%,與原含水率89%相比,污泥體積為原體積的(1-89%)/(1-78.8%)=52%,體積減少48%。原含水率89%的濕污泥產(chǎn)量10m3/d,污泥運輸及后續(xù)填埋或焚燒處置費用按200元/m3計算,每年減少外排污泥運輸費用為365天×(10×0.48)m3/d×200元/m3=35萬元。同時,僅從污泥減容和節(jié)省堆放土地考慮環(huán)保效益和社會效益也是十分顯著的。
5 結(jié)論
含油污泥脫水與氣浮組合工藝經(jīng)實踐充分證明技術(shù)路線成熟可靠、生產(chǎn)操作靈活快捷。尤其在石油化工污水裝置中應(yīng)用,在取得較大經(jīng)濟效益同時社會效益意義重大,相關(guān)行業(yè)可作為技術(shù)借鑒并具有較大的推廣價值。