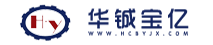
1 離心脫水干化一體技術(shù)(Centridry)
離心脫水干化一體系統(tǒng)主要包括脫水干燥一體機(jī)(又稱脫水干化離心機(jī))、熱介質(zhì)發(fā)生裝置、絮凝劑投配裝置、旋風(fēng)分離器、文丘里冷凝洗滌器、循環(huán)風(fēng)機(jī)及排氣風(fēng)機(jī)、尾氣凈化裝置等設(shè)備。
脫水干化離心機(jī)是系統(tǒng)的核心設(shè)備,濃縮污泥(含水率為95%~99%)與調(diào)配后的絮凝劑分別通過進(jìn)料泵、加藥泵送入脫水干化離心機(jī)進(jìn)口,在離心力作用下,在離心機(jī)轉(zhuǎn)鼓內(nèi)實(shí)現(xiàn)固液分層,固渣由螺旋推料排出轉(zhuǎn)鼓,而澄清液經(jīng)溢流口排出,完成脫水階段;其中澄清液(SS≤500mg/L)通過收集罩收集,排至積水井進(jìn)行后續(xù)處理,而固渣在離心機(jī)轉(zhuǎn)鼓出渣口通過特殊的專利設(shè)計(jì)結(jié)構(gòu)分散成比表面積更大的固相顆粒,提高后續(xù)干化階段的換熱效率。離心機(jī)轉(zhuǎn)鼓外的罩殼為干燥腔體,固相顆粒在干燥腔內(nèi)與熱介質(zhì)發(fā)生器提供的熱空氣(220~350℃)快速進(jìn)行熱交換,完成干燥作用,并由循環(huán)風(fēng)機(jī)產(chǎn)生的循環(huán)風(fēng)帶出離心干化機(jī),完成干化階段。整個(gè)污泥的脫水及干化過程在脫水干化離心機(jī)這一個(gè)設(shè)備中完成。
干燥后的固體粉末和蒸汽(150~280℃)一起被送至旋風(fēng)分離器,完成氣固分離,固體粉末(含水率為8%~40%)則通過輸送系統(tǒng)送至干粉料倉(cāng)或直接裝袋。
旋風(fēng)分離后的氣體(140~270℃)仍然具有一定的熱量,這些熱介質(zhì)大部分會(huì)進(jìn)入循環(huán)管道,回到熱介質(zhì)發(fā)生器中進(jìn)行再次加熱和燃燒“除臭”,充分利用這部分熱能,降低能量損耗。而小部分的氣體通過排氣風(fēng)機(jī)輸送至文丘里冷凝洗滌器,完成氣體的凈化和冷凝,排放至大氣(約80℃)。
2 工藝特點(diǎn)
離心脫水干燥一體化技術(shù)兼具臥螺離心機(jī)和熱干化的特點(diǎn)。首先,臥螺離心機(jī)是在離心力場(chǎng)作用下,懸浮液在轉(zhuǎn)鼓內(nèi)形成環(huán)形液流,固相顆粒在離心力作用下快速沉降到轉(zhuǎn)鼓內(nèi)壁上,由差速器產(chǎn)生轉(zhuǎn)鼓和螺旋輸送器的差速,由螺旋輸送器將沉渣推送到轉(zhuǎn)鼓錐端的干燥區(qū),經(jīng)過螺旋輸送器推料和沉渣離心力的雙向擠壓,使沉渣得到進(jìn)一步擠壓脫水后,從轉(zhuǎn)鼓小端排渣口排出。分離后的清液經(jīng)溢流口排出。該設(shè)備具有連續(xù)高效、設(shè)備體積小、封閉衛(wèi)生條件好、自動(dòng)化程度高、日常維護(hù)工作量小等特點(diǎn)。而熱干化是應(yīng)用較廣泛、較成熟的干化技術(shù),它利用熱能將污泥中的水分變?yōu)樗魵舛⑹?,進(jìn)一步降低污泥含水率,同時(shí)利用高溫滅菌作用,殺死病原體和寄生蟲,加速污泥干燥,避免污泥對(duì)環(huán)境的二次污染,實(shí)現(xiàn)污泥的無害化和資源化利用。
傳統(tǒng)的污泥脫水干化工藝技術(shù)通常采用先對(duì)污泥進(jìn)行機(jī)械脫水(前處理),產(chǎn)生的80%含水率的泥餅再通過存儲(chǔ)、輸送、返混等一系列設(shè)備和設(shè)施送入到干化設(shè)備內(nèi)進(jìn)行污泥干化或深度處理。離心脫水干化一體技術(shù)與傳統(tǒng)的污泥脫水干化技術(shù)不同,它是將污泥的脫水、干燥過程集成在一個(gè)緊湊的設(shè)備空間內(nèi),省去了一系列的附屬設(shè)備,直接涵蓋污泥的前處理和深度處理過程,同時(shí)也大大減少了設(shè)備的投資和運(yùn)行成本。
由于該技術(shù)采用傳熱效率更高的接觸式熱干化法,且污泥顆?;虼似涓苫矢?。
3 案例
3.1 項(xiàng)目概要
南京某化工企業(yè)在生產(chǎn)過程中會(huì)產(chǎn)生有害化學(xué)污泥,若不妥善處理,將對(duì)環(huán)境造成嚴(yán)重污染。該公司若按照原有的設(shè)計(jì)方案,僅對(duì)污泥進(jìn)行機(jī)械深度脫水,其化學(xué)污泥經(jīng)過濃縮處理后,采用機(jī)械壓濾脫水之后再進(jìn)行后續(xù)的危廢處置(填埋或焚燒)。機(jī)械脫水后的污泥含水率仍很高(約75%),其中的水分主要為細(xì)胞內(nèi)部結(jié)合水和部分顆粒吸附水及毛細(xì)水,而且該公司污泥屬于危險(xiǎn)固廢,脫水后污泥后續(xù)處置費(fèi)按當(dāng)?shù)貎r(jià)格為6500元/t,后續(xù)的污泥運(yùn)輸及處置費(fèi)用高昂。因此,該項(xiàng)目主要的目的就是實(shí)現(xiàn)污泥的較大程度減量化,以降低后續(xù)的污泥處置費(fèi)用。
3.2 設(shè)計(jì)選型
根據(jù)該項(xiàng)目的設(shè)計(jì)要求及污泥參數(shù),每天需處理污泥(絕干基)3.6t,則每天處理濃縮污泥量為180m3左右,脫水干化后的污泥為4.5t。
系統(tǒng)主要技術(shù)參數(shù):處理量為7.5m3/h,絕干泥量為150kg/h,蒸發(fā)水量為480kg/h,燃料為0#柴油,循環(huán)介質(zhì)溫度為220~250℃,循環(huán)風(fēng)量為17000~20000m3/h,轉(zhuǎn)速為3900r/min,出粉含水率≤20%,濾液SS≤500mg/L,干粉溫度≤70℃,排放廢氣溫度≤40℃。
3.3 運(yùn)行成本
根據(jù)系統(tǒng)配套設(shè)備的裝機(jī)功率及處理過程中的熱能、水、絮凝藥劑的消耗等費(fèi)用,結(jié)合詳細(xì)的工藝計(jì)算(包括物料平衡和熱量平衡等),分析了該項(xiàng)目的運(yùn)行成本。運(yùn)行費(fèi)用按照處理1m3含水率為98%的濃縮污泥計(jì)算,雖然污泥是在一個(gè)設(shè)備中完成了整個(gè)脫水及干化階段,但為了便于與傳統(tǒng)機(jī)械脫水的運(yùn)行費(fèi)用進(jìn)行分析比較,也將其費(fèi)用分解為機(jī)械脫水及熱干化兩部分。
機(jī)械脫水階段處理1m3含水率為98%的濃縮污泥費(fèi)用為5.45元,與其他機(jī)械脫水設(shè)備費(fèi)用相當(dāng),熱干化階段處理對(duì)應(yīng)的污泥至20%含水率,費(fèi)用為24.69元,所以整個(gè)脫水干化階段所需費(fèi)用約為30.14元,根據(jù)該項(xiàng)目工藝設(shè)計(jì)參數(shù),每天污泥處理的絕干泥量為3.6t,處理費(fèi)用為5425.2元/d。
3.4 經(jīng)濟(jì)分析
按當(dāng)?shù)匚U處置費(fèi)用為6500元/t計(jì)算,后續(xù)處置費(fèi)用為29250元;若該項(xiàng)目采用原來的機(jī)械脫水工藝設(shè)計(jì)方案,每天處理的絕干泥量同樣為3.6t,而產(chǎn)生的脫水污泥總量卻為14.4t,雖然每天的處理費(fèi)用只考慮脫水部分,約為981元/d,但后續(xù)處置費(fèi)用卻為93600元。該項(xiàng)目干化后的污泥為脫水后污泥的31.25%,減量化明顯;另外,每天的污泥干化費(fèi)用增加了約4444.2元,但后續(xù)處置費(fèi)用卻減少了64350元,可大幅降低企業(yè)的運(yùn)行成本。
4 結(jié)論
我國(guó)危險(xiǎn)固廢源頭產(chǎn)生量大、危害性大、不易處理的現(xiàn)狀難以在短時(shí)間內(nèi)得到扭轉(zhuǎn),源頭減量控制是較基本的方法。污泥離心脫水干化一體技術(shù)在該領(lǐng)域具有技術(shù)和經(jīng)濟(jì)雙重可行性,是一種新型的污泥減量化處理工藝,其安全可靠、工藝運(yùn)行穩(wěn)定,運(yùn)行環(huán)境封閉衛(wèi)生,操作簡(jiǎn)單、自動(dòng)化程度高,工藝簡(jiǎn)明、占地空間小,維護(hù)成本低等特點(diǎn)使其具有了較大的推廣應(yīng)用價(jià)值。另外,其干燥后污泥含水率低至10%以下,較大程度地進(jìn)行污泥減量化、穩(wěn)定化,更使得污泥的后續(xù)處置方式更靈活,也極大地降低了后續(xù)處置的難度及成本,尤其適用于危險(xiǎn)固廢行業(yè)。