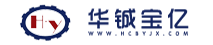
1 前言
臥式螺旋卸料沉降離心機是一種連續(xù)操作的、利用離心沉降原理分離懸浮液的離心機,可在全速運轉(zhuǎn)時連續(xù)進行進料、沉降、分離、卸料操作。具有自動化程度高、生產(chǎn)能力大、運行穩(wěn)定、清潔無污染、應用范圍廣等優(yōu)點。廣泛應用于化工、制藥、食品、輕工、造紙、礦山及環(huán)保等工業(yè)部門。鹽鈣聯(lián)產(chǎn)裝置采用獨有的MVR熱泵鹽鈣聯(lián)產(chǎn)工藝,該裝置安裝了一臺沉降離心機,在使用過程中出現(xiàn)一些問題,值得大家總結(jié)與借鑒。
2 沉降離心機工作原理及適用分離范圍
2.1 沉降離心機工作原理
沉降離心機結(jié)構(gòu)主要由差速器、螺旋、轉(zhuǎn)鼓、罩殼、機座、潤滑系統(tǒng)、主電機以及氣路系統(tǒng)組成。其工作原理是:懸浮液由中部的進料管進入全速運轉(zhuǎn)的轉(zhuǎn)鼓內(nèi),由于高速旋轉(zhuǎn)產(chǎn)生的離心力場的作用,使懸浮液中密度較大的沉渣(重相)沉積在轉(zhuǎn)鼓的內(nèi)壁上,與轉(zhuǎn)鼓作相對運動的螺旋葉片不斷地將沉積在轉(zhuǎn)鼓內(nèi)壁上的固相顆粒刮下并推出排渣口。而密度較小的清液(輕相)則處于沉積層的內(nèi)側(cè),通過螺旋的葉片所形成的螺旋型通道流向轉(zhuǎn)鼓的柱段由溢流口溢出。從而實現(xiàn)密度相差的液-固兩相的分離。
螺旋與轉(zhuǎn)鼓之間的相對運動是由差速器實現(xiàn)的,差速器的外殼與轉(zhuǎn)鼓相接,輸出軸與螺旋相接,輸入軸與電機相聯(lián)。電機帶動轉(zhuǎn)鼓旋轉(zhuǎn)的同時也帶動了差速器輸入軸的旋轉(zhuǎn),其輸出軸按一定的速比將扭矩傳遞給螺旋,實現(xiàn)了離心機對物料的連續(xù)分離過程。
2.2 沉降離心機適用分離范圍
(1)當液相粘度較小,固相顆粒度較大時,要求固、液比重差≥0.05g/cm3(固重、液輕)。
(2)當液相粘度較小,固、液比重差較大時(比重差≥1g/cm3)時,要求固相顆粒≥5μm。
(3)當液相粘度較大或固液比重較小并且固相顆粒很細小時,將影響分離效果,甚至不適用。
(4)當固相顆粒易破損時,也將影響分離效果。
3 沉降離心機在鹽鈣聯(lián)產(chǎn)中的作用
3.1 鹽鈣聯(lián)產(chǎn)工藝簡介
鹽鈣聯(lián)產(chǎn)裝置是以高鈣鹵水為原料,生產(chǎn)氯化鈉與氯化鈣兩種產(chǎn)品,其生產(chǎn)工藝可分為四個主要工序:四效強制預熱、兩級MVR蒸發(fā)制鹽、三效鈣液濃縮及兩效高溫制鈣工序。其原理是利用氯化鈉與氯化鈣在溶液中的溶解度隨溫度升高時的變化趨勢不同,鹵水經(jīng)四效強制預熱工序和MVR蒸發(fā)濃縮后,NaCl蒸發(fā)結(jié)晶析出,經(jīng)過離心分離后作為散濕鹽產(chǎn)品。MVR排出的含CaCl2母液經(jīng)三效鈣液濃縮工序及兩效高溫制鈣工序后,排出高濃度鈣液經(jīng)冷卻結(jié)片后,進入干燥、包裝得到二水氯化鈣產(chǎn)品。
3.2 料液特性
隨著鈣液不斷濃縮,氯化鈣濃度越來越高,當濃縮到42%濃度設計參數(shù)如下:溫度110℃,固液比7%,CaCl2含量619g/L,NaCl含30g/L,CaSO4含量3.1~4.3g/L,混合料液密度1.52t/m3,固體鹽密度2.1t/m3,清液密度1.46t/m3,粘度12cP。該裝置的原料為鈣型鹵水,其主要成分為:NaCl 250~260g/L,CaCl2 60~70g/L,CaSO4 0.6~1g/L。因此在氯化鈣的生產(chǎn)中,其主要雜質(zhì)是固體鹽和硫酸鈣顆粒,而隨著鈣液濃度越來越高,鹽與硫酸鈣結(jié)晶顆粒也會越來越細。42%鈣液有如下特點:
3.2.1 溫度高、腐蝕性大
氯化鈣的腐蝕性比較強,隨著其濃度與溫度的升高,腐蝕性進一步增加。
3.2.2 固、液相密度差小
據(jù)以上參數(shù)測算,此處料液固、液密度差0.7t/m3,低于礦山、冶金,以及其他化工行業(yè),查相關(guān)資料,如制鹽行業(yè)鹵水凈化中鹽泥脫水工序,混合料液的固液密度差為0.9t/m3,純堿行業(yè)水平帶濾機進料料液的固液密度差為0.9t/m3。
3.2.3 料液粘度相對較大、固體顆粒粒徑區(qū)別
此處料液粘度高達12cP,固相硫酸鈣的粒徑細(小于10μm)占比80~85%。固相氯化鈉粒徑相對較大,根據(jù)過濾試驗數(shù)據(jù),粒徑發(fā)布如下:粒徑大于147μm占60~87%,在30~147μm區(qū)間占8~30%,30μm以下占5~10%。
3.3 沉降離心機在此工藝中的作用
沉降離心機設置在氯化鈣含量達42%的工藝點后面,其目的是分離掉料液中含有的固體鹽和固體硫酸鈣以保證清液的質(zhì)量,然后再對固體鹽進行回收。
4 沉降離心機在鹽鈣聯(lián)產(chǎn)中的使用狀況
4.1 分離鹽的效果遠遠優(yōu)于分離硫酸鈣的效果
沉降離心機運行一段時間后,對進料前后料液取樣分析,結(jié)果如下:
(1)沉降離心機分離后的硫酸鈣含量遠遠高于設計值,按設計值沉降離心機將分離掉79%硫酸鈣,結(jié)果只分離了40%。
(2)沉降離心機分離后的氯化鈉含量超過設計值,說明沉降離心機已將料液中絕大部分固形氯化鈉分離掉。
4.1.1 調(diào)整沉降式離心機堰板高度和沉降式離心機運行頻率,提高分離效果
沉降式離心機的分離效果,主要就是調(diào)整頻率及液相堰板高度。對沉降式離心機頻率在35Hz到48Hz范圍內(nèi)分頻段運行;堰板高度從圍堰距離60mm逐步調(diào)整至28mm,每調(diào)整5mm運行一段時間,檢測分析分離效果,當調(diào)整到28mm時,分離母液量較小滿足不了生產(chǎn)需求。堰板調(diào)整到45mm運行,頻率調(diào)整至48Hz,沉降式離心機的分離后清液中硫酸鈣含量能夠達到3~4g/L。
4.1.2 調(diào)整后,分離硫酸鈣效果有了提高,但是存在缺點
增加堰板高度和提高沉降離心機運行頻率,雖然提高了沉降離心機分離效果,但堰板高度增加導致了沉降離心機清液量減少,固相中含液量增加。清液量減少必然導致鈣產(chǎn)量降低;而固相中含液量增加按工藝流程又會將高濃度鈣液隨鹽漿回收系統(tǒng)返回流程前端,形成物料循環(huán)往復,一定程度上增加了系統(tǒng)動力消耗,同時也造成部分熱量前移,系統(tǒng)效率下降。適當減小堰板高度和降低沉降離心機頻率,并不影響沉降離心機分離鹽的效率,因此可按經(jīng)濟的方式調(diào)整運行沉降離心機。
4.2 解決硫酸鈣超標的方法
后期通過攻關(guān),采用其他沉降分離工藝,解決了硫酸鈣偏高的問題。
4.3 沉降離心機運行可靠性
沉降離心機在鹽鈣聯(lián)產(chǎn)運行中,總體穩(wěn)定,但由于該處料液高溫、高濃度,腐蝕性特別強,出現(xiàn)幾次較嚴重故障,影響生產(chǎn)正常穩(wěn)定運行。其問題主要表現(xiàn)如下:
(1)轉(zhuǎn)鼓加強筋腐蝕。
(2)機頭空心軸腐蝕變形。
(3)螺旋輸送器進料空心軸腐蝕變形。
(4)螺旋輸送器葉片腐蝕磨損。
(5)機殼內(nèi)積塊鹽,導致固相斗堵,機件磨損,機體振動,同時導致機器負荷增加,差速器卡死。
上述現(xiàn)象大部分與該料液的特性有關(guān),鑒于沉降離心機在鹽鈣聯(lián)產(chǎn)中的重要作用,聯(lián)合沉降離心機廠家吸取上述教訓,作如下改進:
(1)所有與物料接觸的零部件由原來用的TA2升級為TA10。
(2)與物料接觸的承載件材質(zhì)由原來用的TA2升級為TC4。
(3)機殼增加沖洗水,刷車沖洗。
沉降離心機改造升級后,運行穩(wěn)定,投運一年未發(fā)生任何影響生產(chǎn)的故障,停機檢查與鈣液接觸的部件以及與鈣液接觸的承載件,腐蝕磨損情況良好;機殼內(nèi)也未發(fā)現(xiàn)積塊鹽現(xiàn)象。
5 結(jié)束語
沉降離心機在鹽鈣聯(lián)產(chǎn)工藝中是不可或缺的核心設備,雖然不能高效分離料液中極細硫酸鈣晶體,但更便于后續(xù)工序中鹽漿再回收利用,因此總體使用是很成功的。它在回收系統(tǒng)鹽漿,保證后道系統(tǒng)可靠運行,提高系統(tǒng)產(chǎn)能,降低系統(tǒng)消耗水平等方面起著非常重要作用。