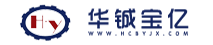
大慶油田某采油廠于1986年建成投產(chǎn),共建有脫水站3座。脫水站油系統(tǒng)全部采用兩段脫水工藝:一段采用游離水脫除器進行油、水初步分離,二段采用復(fù)合電脫水器進一步脫水。脫水處理后,凈化油含水率小于0.3%直接外輸,污水含油量小于1000mg/L進入污水沉降罐。
含油污水進入污水沉降罐后,在重力作用下進行油、水沉降分離。分離出的污水供站外集油系統(tǒng)摻水使用,其余部分輸往含油污水處理站處理后回注;分離出的污油通過收油泵定期回收進入正常生產(chǎn)流程進行脫水處理。但是,自2003年開始,經(jīng)常出現(xiàn)收油時電脫水器運行不穩(wěn)定的情況,主要表現(xiàn)為電脫水器脫水效果不好、含水超標、脫水器電流上升及頻繁放電,導(dǎo)致電場癱瘓,嚴重時甚至燒毀電脫水器的控制系統(tǒng)。至2005年,污水沉降罐內(nèi)的污油已基本無法利用電脫水器進行脫水。
污水沉降罐內(nèi)這種難于處理的污油稱為老化油。為解決老化油問題,有必要研究效率高、流程簡潔、便于操作、處理成本較低的老化油處理工藝技術(shù),確保油氣集輸處理系統(tǒng)安全平穩(wěn)運行。
1 老化油物理及化學(xué)性質(zhì)分析
1.1 老化油含水分析
回收污水沉降罐內(nèi)老化油,用80℃恒溫水浴加熱,經(jīng)自然沉降并冷卻至室溫,去掉沉積水后,采用離心法分析上部“渣油”狀老化油含水率。在所取樣品中,老化油含水率低至21.42%,高達28.28%,具體如下表所示:
取樣序號 | 老化油量/mL | 游離水質(zhì)量/g | 乳化老化油質(zhì)量/g | 乳化水質(zhì)量/g | 乳化油含水率/% |
1 | 150 | 3.0 | 130.697 | 28 | 21.42 |
2 | 150 | 4.5 | 129.540 | 29 | 22.39 |
3 | 200 | 8.0 | 171.587 | 43 | 25.06 |
4 | 250 | 17.6 | 208.644 | 59 | 28.28 |
1.2 老化油硫化物含量分析
利用離心機對老化油樣品進行離心處理,老化油分成3層:上層是黑色的原油層,中間是水層,下部是黑色的機械雜質(zhì)。將下層的黑色機械雜質(zhì)分離出來,用能譜儀分析,確定其為FeS顆粒。
取老化油及油水界面層樣品,測試其硫化物及SRB(硫酸鹽還原菌)含量。測試結(jié)果:油水界面層中硫化物含量為103mg/L,SRB含量為7×105個/mL;老化油中硫化物含量為156mg/L,SRB含量為2×105個/mL。
1.3 擊穿電壓和界面張力測試
將老化油與凈化油按不同比例混合,配置不同FeS含量的油樣。對混合油樣進行擊穿電壓和界面張力測試,測試溫度50℃,測試結(jié)果如下表所示:
混合樣中老化油比例/% | Fes含量/mg/L | 擊穿電壓/V | 界面張力/mN/m |
0 | 0.2 | 44500 | 29 |
10 | 16.0 | 31000 | 42 |
30 | 50.0 | 17500 | 49 |
50 | 79.0 | 12500 | 51 |
70 | 108.0 | 9800 | 62 |
90 | 141.0 | 6500 | 73 |
100 | 156.0 | 3500 | 81 |
由上表可以看出,隨著FeS含量的增加,擊穿電壓降低,界面張力增加。凈化油擊穿電壓為44500V,界面張力為29mN/m,而老化油的擊穿電壓僅為3500V,界面張力高達81mN/m。
2 老化油處理工藝技術(shù)
2.1 熱化學(xué)脫水工藝技術(shù)
將老化油加熱到一定的溫度,并在老化油中加入適量的破乳劑。破乳劑吸附在油水界面膜上,降低油水界面薄膜的表面張力,從而破壞乳狀液的穩(wěn)定性,改變?nèi)榛旱念愋?,以達到油、水分離的目的。
利用1000m3立式金屬罐一座,建成獨立的老化油熱化學(xué)處理系統(tǒng)。針對老化油中富含FeS顆粒、導(dǎo)電性強、表面張力大等問題,研制了高效老化油破乳劑,破乳劑中含有硫化物去除劑配方。
2.1.1 運行參數(shù)
加藥量3000mg/L;處理溫度75~80℃;脫水后原油含水率≤5%;脫水后污水含油量≤1000mg/L。
2.1.2 流程說明
利用收油泵(流量30m3/h,揚程60m)回收污水沉降罐內(nèi)老化油,加熱后進入1000m3老化油罐,同時加入老化油破乳劑;啟動老化油罐前循環(huán)泵(流量50m3/h,揚程60m),循環(huán)加熱老化油,以保證老化油溫度達到80℃以上,同時,確保老化油與老化油破乳劑充分混合;老化油經(jīng)過一段時間的靜止沉降后,將脫出的游離水從老化油罐底部出水口回收至污水沉降罐,由于油水界面層主要是不溶于水也不溶于油的FeS顆粒懸浮物,遇油水界面層需切換流程外排;通過撈油化驗油水界面層上部老化油含水,若含水小于5%,則啟動收油泵收油,并將回收原油摻入外輸管道外輸。
若老化油溫度下降較快,但含水仍較高,則需要重新啟動循環(huán)泵循環(huán)加熱,重復(fù)以上過程。
2.2 離心脫水工藝技術(shù)
熱化學(xué)脫水主要采用重力沉降法脫水,離心脫水則以離心分離替代重力沉降,從而提高油、水分離的速度和效果。通過現(xiàn)場試驗,確定采用兩級離心分離技術(shù)處理老化油。
離心分離裝置主要由臥螺式離心分離系統(tǒng)、碟片式離心分離系統(tǒng)和加藥系統(tǒng)三部分組成。老化油首 入臥螺式離心分離機,在絮凝劑的作用下實現(xiàn)固、液分離,分離出來的含水油進入碟片式離心機,在破乳劑的作用下實現(xiàn)進一步脫水。該處理方式的創(chuàng)新點是在較低的轉(zhuǎn)速下實現(xiàn)固、液分離,在較高的轉(zhuǎn)速下實現(xiàn)油、水分離。
2.2.1 設(shè)備及運行參數(shù)
臥螺式離心機轉(zhuǎn)速3500r/min,功率35kW,處理量5m3/h;碟片式離心機轉(zhuǎn)速6000r/min,功率26kW,處理量5m3/h。
加藥量20mg/L;處理溫度70℃;脫水后原油含水率≤0.3%;脫水后污水含油量≤50mg/L。
2.2.2 流程說明
用收油泵將老化油回收至1000m3老化油罐,通過循環(huán)泵循環(huán)加熱,將老化油升溫至試驗溫度,然后進入臥螺式離心機處理,脫除的固體雜質(zhì)直接裝袋運送至質(zhì)量安全環(huán)保部門指定地點,含水油進入碟片式離心機脫水;碟片式離心機出水進入凈化水罐,出油進入凈化油罐,排渣重新進入臥螺式離心機處理。
若碟片式離心機出油、出水指標較差,則將凈化水罐中的水輸入臥螺式離心機,凈化油罐中的油輸回至老化油罐循環(huán)加熱再處理;若碟片式離心機出油、出水指標合格,則將水輸回至本站污水沉降罐,油直接外輸。
2.3 微生物處理技術(shù)
老化油中的硫化物及SRB含量較高。SRB是一種硫化細菌,它能分解硫酸鹽,產(chǎn)生的代謝產(chǎn)物為H2S、HS-或S2-,H2S會腐蝕金屬管道和設(shè)備,生成Fe2+,S2-與Fe2+反應(yīng)生成FeS,大大增強了原油的導(dǎo)電性,從而導(dǎo)致電脫水器運行不穩(wěn)。
基于這一認識,采用一種新的技術(shù)思路,即,采用微生物來抑制和消除老化油中的SRB及硫化物。其主要機理是利用生物競爭淘汰法來消除老化油中的SRB,并通過細菌作用,將SRB產(chǎn)生的FeS氧化成SO42-。
通過室內(nèi)試驗,從SOB菌、B.B菌等多種菌中篩選了TD菌種處理老化油。TD菌株是嚴格自養(yǎng)和兼養(yǎng)性厭氧菌,細胞呈球桿狀,菌體大小0.3~1.5μm,單個、成對或短鏈狀排列,運動活潑,無芽孢。
2.3.1 運行參數(shù)
加藥量:60mg/L;處理溫度:55℃;生物作用時間6d;脫水后原油含水率≤0.3%(電脫水器出油);脫水后污水含油量≤500mg/L。
2.3.2 流程說明
利用1座200m3凈化油緩沖罐作為老化油反應(yīng)罐,利用收油泵回收污水沉降罐內(nèi)老化油(提前用70℃摻水將老化油預(yù)熱),同時加入TD菌種;TD菌種與老化油在老化油反應(yīng)罐中發(fā)生作用,靜止沉降。老化油反應(yīng)罐由罐底伴熱盤管加熱維溫,罐內(nèi)溫度呈緩慢下降趨勢。4d后開始取樣,測試老化油酸堿性,若老化油顯中性,則利用污油泵將老化油輸至游離水脫除器進入正常流程處理。
3 老化油處理技術(shù)影響因素分析
3.1 熱化學(xué)脫水技術(shù)影響因素分析
恒溫水浴,脫水溫度分別為60℃、70℃、80℃,脫水試瓶若干,試驗藥劑分別為常規(guī)的油溶性破乳劑、水溶性破乳劑,以及老化原油處理劑(ALDT),加藥量分別為被處理油樣的1%、3%、5%。當(dāng)脫水溫度為60℃時,破乳劑脫水效果很差。
隨著溫度上升,脫水速度加快;油田常規(guī)使用的破乳劑對老化油的脫水作用效果甚微,ALDT型老化油處理劑脫水速度較快,脫水效果較好。因此,溫度和破乳劑是影響熱化學(xué)脫水效果的主要因素。
3.2 離心脫水技術(shù)影響因素分析
從污水沉降罐回收老化油至1000m3老化油沉降罐,通過循環(huán)加熱,1000m3老化油沉降罐內(nèi)老化油溫度緩慢上升,每小時升溫約0.5℃。當(dāng)油溫升至50℃時,調(diào)整加熱爐燃燒器開度,保持罐內(nèi)油溫不變,試驗不同絮凝劑、破乳劑加入量的脫水效果;然后,油溫每升高5℃,重復(fù)以上試驗,摸索較佳生產(chǎn)運行參數(shù)。
溫度及加藥量對離心脫水工藝中臥螺離心機和碟片式離心機脫水效果的影響規(guī)律見下表:
處理溫度/℃ | 臥螺式離心機 | 碟片式離心機 | |||
絮凝劑加入量/mg/L | 固體含油量/% | 破乳劑加入量/mg/L | 原油含水率/% | 污水含油量/mg/L | |
50 | 100 | 5.0 | 100 | 26.3 | 360 |
200 | 4.6 | 200 | 19.5 | 170 | |
300 | 3.7 | 300 | 16.4 | 160 | |
500 | 3.1 | 500 | 10.2 | 130 | |
1000 | 2.3 | 1000 | 6.5 | 80 | |
55 | 100 | 4.5 | 100 | 17.5 | 210 |
200 | 3.7 | 200 | 10.5 | 120 | |
300 | 3.0 | 300 | 5.0 | 75 | |
500 | 2.3 | 500 | 2.0 | 50 | |
1000 | 2.2 | 1000 | 1.8 | 50 | |
60 | 20 | 2.0 | 20 | 5.0 | 50 |
50 | 1.8 | 50 | 4.7 | 40 | |
80 | 1.6 | 80 | 4.6 | 35 | |
100 | 1.5 | 100 | 4.6 | 30 | |
65 | 20 | 1.9 | 20 | 2.3 | 50 |
50 | 1.6 | 50 | 2.4 | 43 | |
80 | 1.4 | 80 | 2.5 | 37 | |
100 | 1.3 | 100 | 2.9 | 35 | |
70 | 20 | 1.6 | 20 | 0.28 | 45 |
50 | 1.4 | 50 | 0.26 | 36 | |
80 | 1.3 | 80 | 0.25 | 35 | |
100 | 1.2 | 100 | 0.24 | 33 |
由上表可以看出,在相同的溫度下,隨著加藥量的增加,處理效果提高。處理溫度大于等于60℃后,在較小的加藥量下就有較好的脫水效果,當(dāng)處理溫度為70℃,加藥量為20mg/L時,可以直接達到商品油外輸?shù)囊?。因此,溫度是影響離心脫水效果的主要因素。
3.3 微生物處理老化油技術(shù)影響因素分析
3.3.1 TD菌種濃度對硫化物及細菌的影響規(guī)律
采集污水沉降罐的老化油,按不同比例依次投加TD制劑,放置于50℃恒溫水浴中。共進行10d微生物處理試驗,每隔2d分別對樣品中的SRB細菌和硫化物進行測定。從測試結(jié)果可以看出,加藥濃度大于等于60mg/L時,藥劑對老化油除硫化物和殺菌效果明顯,較佳作用時間為6d,老化油中硫化物去除率可達90%,細菌去除率可達99%。
3.3.2 TD菌種濃度對擊穿電壓的影響規(guī)律
每隔2d取生化處理試驗中的老化油,裝入試驗器中,進行擊穿電壓測試。從測試結(jié)果可以看出,在加藥濃度60mg/L條件下,反應(yīng)6d后,老化油擊穿電壓提高了643%。
3.3.3 TD菌種濃度對界面張力的影響規(guī)律
每隔2d取生化處理試驗中的老化油,利用表面張力儀對界面張力進行測試,從測試結(jié)果可以看出,在加藥濃度60mg/L條件下,反應(yīng)6d后,老化油界面張力降低了58%。
3.3.4 環(huán)境因素對TD菌種處理老化油效果的影響
為了確定TD菌種的適用范圍,測試了pH值、溫度對TD菌種活性的影響規(guī)律。
(1)pH值對老化油處理效果的影響
采集污水沉降罐中的老化油,測試pH值為7.32,分別用HCl、NaOH調(diào)制不同的pH值,然后投加TD制劑,投藥濃度為60mg/L。在55℃恒溫條件下處理時間為6d,測試硫化物及細菌的含量。從測試結(jié)果可以看出,在除硫化物方面,較佳pH值范圍為6.0~8.5;綜合考慮,微生物作用于老化油的pH值范圍為6.0~8.5。
(2)溫度對老化油處理效果的影響
采集污水沉降罐中的老化油,投加濃度為60mg/L的TD制劑后,放置于不同溫度的恒溫水浴中,測試硫化物的變化情況。從測試結(jié)果可以看出,在40℃和90℃時,老化油中硫化物含量下降緩慢,說明TD菌種在低溫、高溫時活性降低。在50~80℃試驗條件下,隨著處理時間的延長,硫化物含量逐漸降低,當(dāng)處理時間超過6d時,硫化物降低幅度趨于平緩。由此可知,微生物活性在50~80℃范圍內(nèi)受溫度影響不大。
試驗說明,TD微生物作用于老化油的較佳加藥量為60mg/L,處理溫度為55±5℃,較佳靜止沉降時間為6d??紤]到現(xiàn)場生產(chǎn)情況的復(fù)雜性,為保證處理效果,可適當(dāng)提高加藥量。
4 老化油處理工藝適應(yīng)性分析
4.1 老化油處理工藝技術(shù)經(jīng)濟對比
熱化學(xué)脫水工藝、離心脫水工藝、微生物處理技術(shù),這3種老化油處理工藝技術(shù)經(jīng)濟對比見下表:
對比項目 | 熱化學(xué)脫水 | 離心脫水 | 微生物處理技術(shù) |
運行參數(shù) | 破乳劑加入量3000mg/L; 處理溫度75~80℃; 處理時間12~20d | 破乳劑加入量20mg/L; 絮凝劑加入量20mg/L; 處理溫度70℃; 處理時間:即時 | 微生物投加量60mg/L; 破乳劑投加量20mg/L; 處理溫度55℃; 處理時間6d |
處理指標 | 脫水后原油含水率5%; 脫水后污水含油量1000mg/L | 脫水后原油含水率0.3%; 脫水后污水含油量50mg/L; 污泥中含油量2% | 脫水后原油含水率0.3%; 脫水后污水含油量500mg/L |
處理成本/元/m3 | 155 | 24 | 5 |
4.2 老化油處理工藝適應(yīng)性
熱化學(xué)脫水工藝運行費用高,處理周期長,但流程簡單,技術(shù)成熟,適用于老化油產(chǎn)生數(shù)量較少的站場,特別是現(xiàn)場有富余沉降罐的站場,流程基本不需改造。
微生物處理技術(shù)運行費用較低,但是,需要和電脫水器配套進行脫水,同時,需要控制老化油摻入量。因此,該技術(shù)僅適用于老化油產(chǎn)生數(shù)量少的脫水站。
對于現(xiàn)場老化油數(shù)量較多的戰(zhàn)場,建議采用兩級離心分離技術(shù)。在低轉(zhuǎn)速下有效去除老化油中的固體雜質(zhì),高轉(zhuǎn)速下實現(xiàn)油、水分離。該技術(shù)雖一次性投入較高,但處理速度快,運行費用相對較低,處理后的老化油可以達到凈化油的指標直接外輸。
5 結(jié)論及建議
自2005年開始,在十年的時間里,試驗了多種老化油處理工藝,其中,熱化學(xué)脫水、離心脫水和微生物處理技術(shù)在現(xiàn)場取得了較好的應(yīng)用效果。但是,各種老化油處理工藝僅僅是一種應(yīng)急措施,應(yīng)從根源上解決老化油的產(chǎn)生,建議:
(1)加強生產(chǎn)管理和改造力度,杜絕管道穿孔、跑、冒問題,減少油泥進入生產(chǎn)系統(tǒng)的可能性;對聯(lián)合站污水沉降罐增建連續(xù)收油裝置,及時回收污油,避免污油長期存放形成老化油。
(2)加強科研公關(guān)力度,采用物理方式對油井、管道、容器進行清蠟、解堵、除垢,減少各種酸的應(yīng)用,以減少老化油的形成?;蛘咴诩?、污水、注水系統(tǒng)加注微生物抑制劑,從根本上避免老化油的產(chǎn)生。