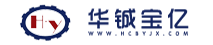
某石化公司腈綸廠應(yīng)用硫氰酸鈉溶液作為腈綸生產(chǎn)過程的溶劑,在生產(chǎn)中循環(huán)利用,由回收裝置進行凈化、提濃?;厥昭b置結(jié)晶工序應(yīng)用離心機分離沉降槽底部沉積的硫酸鈉晶體,實現(xiàn)固液分離,共有2臺臥式螺旋卸料沉降離心機。由于離心機固相硫酸鈉作為廢料外運處理,其中含有較多的硫氰酸鈉,造成一定量的損耗,改善離心機的分離效果可以節(jié)約生產(chǎn)成本,減少硫氰酸鈉的損耗。
1 離心機分離效果的影響因素
1.1 離心機設(shè)備
臥式螺旋卸料沉降離心機為柱型,由2個獨立回轉(zhuǎn)的轉(zhuǎn)子組成,1個為圓柱-圓錐型無孔轉(zhuǎn)鼓,另1個為帶有螺旋葉片的螺旋推進器,二者同軸水平地套裝在一起。
離心機的轉(zhuǎn)筒為逆時針旋轉(zhuǎn),轉(zhuǎn)鼓與其內(nèi)的螺旋推進器同心同向旋轉(zhuǎn),轉(zhuǎn)鼓速度稍快于螺旋推進器。當(dāng)硫酸鈉晶體和硫氰酸鈉溶液組成的懸浮液由進料管導(dǎo)入螺旋推進器內(nèi)腔,經(jīng)分配口進入轉(zhuǎn)鼓的沉降區(qū)(圓柱型部分),在離心力作用下,比重較大的固相物沉積在轉(zhuǎn)鼓內(nèi)壁,被螺旋推進器推出沉降區(qū),通過干燥區(qū)由轉(zhuǎn)鼓小端排出,被澄清的分離液沿螺旋推進器通道流向轉(zhuǎn)鼓的大端由溢流孔排出,懸浮液的固、液兩相得到分離。
1.2 物料的生產(chǎn)控制情況影響分離效果
1.2.1 蒸發(fā)線出料液的影響
結(jié)晶系統(tǒng)進料的硫酸鈉含量主要受晶種量的影響。晶種量偏小,硫酸鈉因晶核少不易析出,使離心機固液相分離效果變差,晶種量大,硫酸鈉析出晶體較大,有許多粒度偏小,沉降槽底部硫酸鈉含量變高,料液粘度變大,易堵塞離心機,并且進料量被迫提高,離心分離效果變差??刂坪侠淼木ХN濃度,保證硫酸鈉晶體的析出,對離心機分離效果影響較大,經(jīng)過實踐總結(jié),蒸發(fā)線出料硫酸鈉含量控制范圍為0.9%~1.2%。
1.2.2 離心機進料量的影響
結(jié)晶系統(tǒng)沉降槽底部硫酸鈉含量,即為離心機進料的硫酸鈉含量,受離心機進料量影響較大,生產(chǎn)中靠調(diào)節(jié)離心機進料量維持沉降過程的穩(wěn)定,獲得沉降槽頂部硫酸鈉含量合格的溢流液。但離心機進料量過大,導(dǎo)致晶體在轉(zhuǎn)筒中的沉降時間不夠,離心分離效果變差。達到離心機設(shè)計中的分離條件的前提是:固相粒子沉降到轉(zhuǎn)鼓壁上時間必須小于顆粒在轉(zhuǎn)鼓內(nèi)的停留時間。離心機進料量過小,沉降槽底部硫酸鈉含量上升很快,容易造成沉降槽溢流液質(zhì)量不合格,料液粘度變大,堵塞管線,還可能導(dǎo)致晶種量偏大,繼而出現(xiàn)結(jié)晶系統(tǒng)的生產(chǎn)波動。生產(chǎn)中,沉降槽底部硫酸鈉含量控制為10%~20%,沉降槽的沉降效果和離心機的固液相分離效果變好。
1.2.3 結(jié)晶系統(tǒng)進料其它控制參數(shù)的影響
結(jié)晶系統(tǒng)進料pH值、溫度、硫氰酸鈉濃度對溶液中的硫酸鈉溶解度有很大的影響。pH值、溫度偏低控制,使硫酸鈉溶解度下降,有利于硫酸鈉的析出。硫酸鈉溶解度隨硫氰酸鈉濃度上升而下降。
2 改善離心機分離效果的方法
2.1 設(shè)備方面的改進
該腈綸廠自2013年以來,為提高離心機分離固相的干度,減少硫氰酸鈉的損耗,在設(shè)備方面采取了3項舉措。
(1)減小差速器的輪徑。提高螺旋推進器的轉(zhuǎn)速,與轉(zhuǎn)鼓的差轉(zhuǎn)速由原來的25r/min調(diào)至10r/min。
(2)減少清洗頻次,提高轉(zhuǎn)鼓清洗效果,適當(dāng)降低離心機進料量。管理上強化每8h必須清洗轉(zhuǎn)鼓1次,清洗離心機內(nèi)腔由每2h清洗1次改為每3h清洗1次。由于清洗時間的適當(dāng)減少,使離心機進料量下降約0.05m3/h,有利于提升分離效果。
(3)根據(jù)分離固相的干度,及時調(diào)整電機頻率。離心機電機頻率控制在37~45Hz,具體的設(shè)定值根據(jù)分離效果調(diào)整,既要保證設(shè)備運行正常,又要保證分離效果。
2.2 工藝方面的改進
工藝方面采取4項改進措施。
(1)根據(jù)蒸發(fā)線出料量和硫酸鈉含量,及時調(diào)整晶種量。控制蒸發(fā)出料硫酸鈉含量,繼而保證結(jié)晶系統(tǒng)進料硫酸鈉含量為0.9%~1.2%,維持良好的沉降效果,保證硫酸鈉晶體的粒徑,有利于離心機的分離。
(2)及時根據(jù)沉降槽底部硫酸鈉含量調(diào)整離心機進料量,維持硫酸鈉含量10%~20%。
(3)將亞硫酸氫鈉溶液(濃度29.5%)改進蒸發(fā)加料液中,通過控制蒸發(fā)出料的pH值,實現(xiàn)結(jié)晶物料pH值為6.0~7.0。
(4)在保證蒸發(fā)線出料濃度的基礎(chǔ)上,將結(jié)晶閃蒸絕壓下限控制(6.5~7.0kPa),使沉降槽料液溫度下降2~3℃,有利于硫酸鈉析出。
3 實施效果
該腈綸廠實施上述改進措施后,離心機分離效果明顯好轉(zhuǎn),離心機分離固相中的NaSCN含量由26%下降至15%,2016年沉降槽溢流液硫酸鈉含量合格率達100%。離心機生產(chǎn)情況見下表:
項目 | 2013年 | 2014年 | 2015年 | 2016年 |
進料量/m3/h | 0.52 | 0.63 | 0.61 | 0.56 |
年運轉(zhuǎn)時間/h | 6448 | 7098 | 7036 | 7665 |
固相產(chǎn)量/t | 1072 | 1256 | 939 | 1041 |
固相NaSCN含量/% | 26.38 | 24.57 | 20.26 | 15.24 |
固相Na2SO4含量/% | 58.44 | 64.39 | 68.72 | 74.36 |
沉降槽溢流合格率/% | 85.71 | 91.72 | 95.03 | 100 |
4 結(jié)束語
該石化公司腈綸廠通過設(shè)備及工藝方面的改進,有效地改善了離心機分離效果,提高了分離固相的干度,降低離心機轉(zhuǎn)鼓與螺旋推進器的差轉(zhuǎn)速,控制合理的晶種濃度,保證硫酸鈉晶體的析出,調(diào)整離心機的負荷,控制沉降槽底部硫酸鈉含量,有利于改善離心機的分離效果。