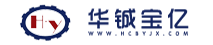
生物工業(yè)中,萃取是一個重要的提取方法和分離混合物的單元操作。萃取法是20世紀40年代興起的一項分離技術,將選定的某種溶劑加入到混合物中,因混合物中的各組分在同種溶劑中的溶解度不同,因此就可將所需提取的組分加以分離出來,這個操作過程叫做萃取。萃取在能源和資源利用、生物和醫(yī)藥工程以及環(huán)境工程和高新材料的開發(fā)等方面面臨著新的機遇和挑戰(zhàn),應用前景廣泛,發(fā)展?jié)摿薮蟆?/span>
若萃取的混合物是液體,則此過程是液-液萃取。常用的萃取方法有溶媒萃取法、雙水相萃取法和超臨界萃取法。若被處理的物料是固體,則此過程稱為液-固萃?。ㄒ卜Q為提取或浸取),即應用溶液將固體原料中的可溶組分提出來的操作。超臨界萃取過程是介于蒸餾和液-液萃取過程之間的分離過程,是利用臨界或超臨界狀態(tài)的流體,使被萃取的物質在不同的蒸汽壓力下所具有的不同化學親和力與溶解能力進行分離、純化的操作。
1 生物工業(yè)萃取設備的選用原則
萃取設備的類型較多,對具體的生產過程選擇適宜的設備,其原則是首先應滿足生產的工藝要求和條件,然后從經濟的角度衡量,使成本降低。為此,需要了解過程的特點、物系的性質,再結合設備的優(yōu)缺點和適用范圍進行初選,以經濟衡算決定。但是,目前對萃取設備的研究還很不充分,經濟衡算所必需的數據尚缺欠,故在選擇時往往要和經驗聯系起來綜合考慮。
(1)對于中、小生產能力來說,可用填料塔、脈沖塔;對較大的處理量,可選用轉盤塔、篩板塔和往復篩板塔,離心萃取機的處理能力相當大。
(2)所需的平衡級數。當所需的理論級數不多(≤3),各種萃取設備都可滿足要求。理論級數較多時,可選篩板塔。再多時,如10~20級,可選用轉盤塔、脈沖塔和往復篩板塔等輸入機械能量的設備。
(3)物料的理化性狀。當兩液體間的界面張力大時,液滴難于分散、易于合并,要求輸入機械能以改善傳質性能;黏度大的物系也有此要求。界面張力小,易于乳化以及密度差很小難于分層的物系,則宜選用離心萃取機,而不宜選用其他輸入機械能的設備。
(4)特殊物性的物系。有較強腐蝕性的物系,宜選用結構簡單的填料塔、脈沖填料塔,對于放射性元素的提取,脈沖塔和混合-澄清槽用得較多。當物系含固體懸浮物或會產生沉淀時,通常需要周期停工以進行清洗,以混合-澄清槽較為適用;往復篩板塔和脈沖塔具有一定的自動清洗能力,也可考慮;填料塔和離心萃取機則不宜采用。
(5)物料的停留時間。當要求萃取時間短,如抗菌素生產等,以離心萃取機為合適。相反,若要求萃取時間長,如伴有慢速反應的物系,則以混合-澄清槽為合適。
2 生物工業(yè)萃取設備的選型
實現組分分離的萃取操作過程由混合、分層、萃取相分離和萃余相分離等組成,工業(yè)生產中常見的萃取流程有單級和多級萃取流程。
2.1 液-液萃取設備選用
液-液萃取設備包括混合設備、分離設備和溶劑回收設備。混合設備是進行萃取操作設備,它要求制液與萃取劑充分混合形成乳濁液,欲分離的生物產品自料液中轉入萃取劑中,分離設備是將萃取后形成的萃取相和萃余相進行分離。溶劑回收設備需要把萃取液中的生物產品與萃取溶劑分離并加以回收,主要用蒸餾設備完成。
2.1.1 混合設備選用
混合設備可分為三種。一種是攪拌罐式混合器,傳統(tǒng)的混合設備的攪拌罐,類似于帶機械攪拌器的密閉式反應罐,可用螺旋槳式或渦輪式攪拌器,罐內設置擋板,罐口頂設置加料管,料液在罐內幾乎處于全混流狀態(tài),使罐內兩液相的平均濃度與出口濃度近似相同,其特點是:裝置簡單,操作方便,但屬于間歇操作,生產能力小,傳質效率較低;第二種是管式混合器,通常采用混合排管,萃取劑及料液在一定流速下進入管道一端,混合后從另一端導出,料液應在管道內停留足夠的時間,并使流動量完全湍流狀態(tài),混合管的萃取效果高于混合罐,且為連續(xù)操作;第三種是噴射式混合器,噴射式混合器有多種形式,器內混合、器外混合及混合孔板式。
2.1.2 分離設備選用
料液萃取的分離主要依靠兩相液體的密度不同,在離心力的作用下,將液體分離。一般采用分離因數很大的碟片高速離心機和管式超速離心機進行分離操作。
2.1.2.1 碟片式離心機選用
碟片式離心機適于分離乳濁液或含少量固體的乳濁液,其結構分為機械傳動裝置、轉鼓、碟片架、碟片和輸送裝置等。此類離心機種類較多,有英國Delaval、德國OEH-10006、OEP-10006型以及國產DRY-400型等。下表列出幾種離心機的技術特性,可供參考。
規(guī)格 | 型號 | ||
DRY-400 | CAk-3 | OEP-10006 | |
轉鼓內徑(mm) | 400 | 330 | 550 |
碟片外徑(mm) | 250 | 400 | |
碟片內徑(mm) | 100 | 120 | |
碟片數(個) | 80~92 | 75 | 150 |
碟片間隙(mm) | 0.8 | 0.8 | |
碟片錐頂角(°) | 80 | ||
轉鼓轉速(r/min) | 6650 | 4620 | 4060 |
分離因數 | 9800 | 3900 | 5040 |
生產能力(m3/h) | 4 | 2.5 | 10 |
電動機功率(kW) | 13 | 3.5 | 11 |
2.1.2.2 管式離心機選用
管式離心機是為避免轉鼓所受過大壓力,保持設備堅固性,同時增加轉速,減少了轉鼓半徑,使轉速得以提高。該機轉鼓上端設有輕、重液排出口,下端的中空軸與轉鼓內腔相通,并通過軸封裝置與進料管相連。管式離心機的轉鼓直徑在200mm以內,一般為70~160mm,其長度與直徑之比一般為4~8。轉鼓的轉速多在10000r/min以上,分離因數可達15000~65000。離心機啟動后,料液由進料管進入轉鼓底部,在轉鼓內從下向上流動的過程中,由于輕、重組分的密度不同而分成內、外兩液層。外層為重液,內層為輕液,到達頂部后,輕液與重液分別從各自的溢流口排出。其清液通過軸周圍環(huán)狀擋板環(huán)溢流而出,而重液則通過轉鼓前端的內徑可更換的環(huán)狀溢流堰外面引出。
特點是結構簡單、緊湊,維修方便,但生產能力小;可分離輕重不同互不溶解的混合液,同時亦可以分離含少量微細固體懸浮物的液固系。管式離心機型號有國產GF-105型、1280型,國外有美國Sharpler型等。
2.1.2.3 立式連續(xù)逆流離心萃取機選用
立式連續(xù)離心萃取機國內外有較多型號,國內生產廠也較多,下表列出二種型號LC-500,ABE-216特性參數,可參考。
內容 | 項目 | |
LC-500 | ABE-216 | |
轉鼓內徑(mm) | 500 | 550 |
轉鼓轉速(r/min) | 4700 | 6408 |
容量(L) | 61 | 70 |
開孔數 | 40~50 | 90~95 |
孔直徑(mm) | 8 | 6~9 |
開孔面積(cm2) | 20~70 | 27~57 |
流道截面積(cm2) | 24.8~57.8,螺旋帶無缺口 | 9.8~23.3,螺旋帶有缺口 |
處理量(L/h) | 4 | 5~6 |
轉鼓存渣量 | 輕重液澄清區(qū)渣滓較少,停車時可用高流水沖走 | 輕重液澄清區(qū)均有渣滓,停車時用高流水沖不出來 |
青霉素萃取收率(%) | 89.5 | 90 |
如對兩種密度差很小液體的萃取分離時,或界面張力很小,而易乳化或黏度很大時,可采用連續(xù)式萃取。連續(xù)逆流離心萃取機是將萃取劑與料液在逆流情況下進行多次接觸和多次分離的萃取設備。
它的主要結構是由11個不同直徑的同心圓筒組成的轉鼓,圓筒上在一端有開孔,位置上下錯開,液體折轉上下流動。4~11筒外壁上均焊有螺旋形導流板,使兩液相間混合與分離時間延長。操作時料液從底部軸周圍的套管進入轉鼓,沿螺旋形通道由內向外順次流經各筒,由外筒經溢流環(huán)到向心泵室排出。萃取劑則由底部的中心管進入轉鼓,流入第10圓筒,從下端進入螺旋形通道,由外向內順次流過各筒,從第1筒經出口排出。
2.1.2.4 傾析式離心機選用
傾析式離心機由德國較早研制出來,如英、日等國公司已將其應用生物技術等領域。其特點是可同時分離重液、輕液和固體,它由圓柱-圓錐形轉鼓、螺旋輸送器、驅動裝置和進料系統(tǒng)等組成。該機與臥式螺旋離心機的區(qū)別為:在螺旋轉子柱的兩端分別配制有調節(jié)環(huán)和分離盤,以調節(jié)輕、重相界面,并在輕相出口處配有向心泵,在泵的壓力作用下,將輕液排出,進料系統(tǒng)上設有中心套管式進料口,使輕、重液二相均從中心進入,固體沉積于轉鼓內壁,借助于螺旋轉子緩慢推向轉鼓錐端,并連續(xù)排出。
2.1.2.5 LUWE型離心萃取器選用
該機是一種立式逐級接觸式離心萃取設備,結構上分為三段。下段是 級混合與分離區(qū),中段是第二級,上段是第三級。每一段的下部是混合區(qū)域,中部是分離區(qū)域,上部是重液相引出區(qū)域,新鮮的萃取劑由第三級加入,待萃取料液則由 級加入,萃取輕液相在 級引出,萃取余液則在第三級引出。
LUWE型離心萃取器的優(yōu)點是:可以靠離心力的作用處理密度差小或易產生乳化現象的物系;設備結構緊湊,占地面積小,效率高。缺點是:動能消耗大,設備費用也較高。
2.2 浸取設備的選用
浸取過程又可稱為固-液萃取,是指在一定作用條件下,用浸出溶劑從固體原料中浸出有效成分的過程。浸取過程中,物質由固相轉移到液相是一個傳質過程。整個過程,固體物料是否需要預處理,物料中溶質是否能快速與溶劑接觸,是影響浸取速度的一個重要因素。浸取設備可分為單級與多級,多級按固液流向又可分為錯流和逆流。按操作方式又有間歇、半連續(xù)和連續(xù)之分。浸取操作廣泛地應用于生物工業(yè)、食品工業(yè)、制藥工業(yè)和冶金工業(yè)中,間歇式浸取器使用較少,工業(yè)生產多以連續(xù)式浸取器為主,下面以連續(xù)式浸取器為重點介紹。
2.2.1 半連續(xù)浸取設備選用
此類設備為一類固定床固液接觸設備,固體原料裝填成固定床靜止不動,萃取劑以一定流量自上而下流經固體將溶質溶出,萃取液在流動過程中濃度增加,自固定床下部排出,其主要設備為萃取塔,有幾種典型設備,即填料萃取塔、轉盤萃取塔和攪拌萃取塔等。
2.2.1.1 篩板萃取塔的選用
篩板萃取塔的結構與氣液傳質設備中的篩板塔類似,輕液從塔的近底部處進入,從篩板之下因浮力作用通過篩孔而被分散;液滴浮升到上一層篩板之下,合并,集聚成輕液層,又通過上層篩板的篩孔而被分散。依此,輕液每通過一層篩板就分散-合并一次,直到塔頂集聚成輕液層后引出。作為連續(xù)相的重液則在篩板之上流過,與輕液液滴傳質,然后沿溢流管流到下一層篩板,逐漸與輕液傳質,一直到塔的底段后流出。萃取塔篩板的特點是溢流管不設置溢流堰。如要求重液作為分散相,需使塔身放在倒轉的位置上,即溢流管改裝在篩板之上成為升液管,使作為連續(xù)相的輕液沿管上升。
工業(yè)上篩板塔間距一般取約300mm,篩板上的篩孔按正三角形排列,通??讖綖?/span>3~8mm,孔間距為孔徑的3~4倍,界面張力較大的物系宜用較小的孔徑,以促使生成較小的液滴。
2.2.1.2 往復篩板萃取塔的選用
往復篩板萃取塔可較大幅度地增加相際接觸面積和提高液體的湍動程度,傳質效率高,流體阻力小,操作方便,生產能力大,在石油化工、食品、制藥和濕法冶金工業(yè)中應用日益廣泛。
往復篩板萃取塔是將若干層篩板按一定間距固定在中心軸上,由塔頂的傳動機構驅動而作上下往復運動。往復振幅一般為3~50mm,頻率可達100/min。往復篩板的孔徑要比脈動篩板的大些,一般為7~16mm。當篩板向上運動時,迫使篩板上側的液體經篩板向下噴射;反之,又迫使篩板下側的液體向上噴射。為防止液體沿篩板與塔壁間的縫隙走短路,每隔若干塊篩板,在塔內壁應設置一塊環(huán)形擋板,往復篩板萃取塔的效率與塔板的往復頻率密切相關,當振幅一定時,在不發(fā)生液泛的前提下,效率隨頻率的增大而提高。
2.2.1.3 轉盤萃取塔的選用
轉盤萃取塔是常用的萃取工業(yè)設備,材料均為不銹鋼,由塔身、上、下分離段和轉軸等組成。用在植物藥液成分的精制,如生物堿、有機酸和黃酮類的提純精制等操作。
轉盤萃取塔,由于轉盤能分散液體,故塔內無需另設噴灑器,只是對于大直徑的塔,液體宜順著旋轉方向從切線進口引入,以免沖擊塔內已經建立起來的流動狀況,轉盤塔的主要結構參數間的關系一般在下述范圍內:塔徑/轉盤直徑=1.5~2.5;塔徑/固定環(huán)開孔直徑=1.3~1.6;塔徑/盤間距=2~8。
萃取操作時,轉盤隨中心軸高速旋轉,其在液體中產生的剪應力將分散相破裂成許多細小的液滴,在液相中產生強烈的渦旋運動,從而增大了相際接觸面積和傳質系數。同時固定環(huán)的存在一定程度上抑制了軸向返混,因而轉盤萃取塔的傳質效率較高。特點有:
(1)轉盤的軸采用無級調速,適應不同的工藝條件。
(2)為適應工藝條件設多個視孔、燈孔,便于清洗和料液成分提純。
(3)轉盤萃取塔結構簡單,傳質效率高,生產能力大。
2.2.2 連續(xù)式多功能提取罐的選用
許多藥材浸取多用此設備,屬于夾套式壓力容器,結構多樣,可用于中藥以及食品、化工等行業(yè)的水煎、溫浸、熱回流、芳香成分提取以及殘渣有機溶媒回收,強制循環(huán)提取、罐組式逆流提取等多種工藝、工序操作,也可在真空情況下操作。
物料經加料口進入罐內,浸出液從活底上的濾板過濾后排出。夾層可通入蒸汽加熱,或通水冷卻。排渣底蓋,可用氣動裝置自動啟閉。為了防止藥渣在提取罐內膨脹,因架橋難以排出,罐內裝有料叉,可借助于氣動裝置自動提升排渣。出渣門上設有不銹鋼絲網,這樣使料渣與浸出液得到了較為理想的分離。設備底部出渣門和上部投料門的啟閉均采用壓縮空氣作動力,由控制箱中的二位四通電磁氣控閥控制氣缸活塞,操作方便。也可用手動控制器操縱各閥門,控制氣缸動作。
主要結構由罐體、出渣門、加料口、提升氣缸、夾層和出渣門氣缸等組成。按設備外形分,有正錐形、斜錐形和直筒形三種形式;按提取方法分,有動態(tài)提取和靜態(tài)提取兩種。
2.3 超臨界萃取設備的選用
超臨界流體萃取是上世紀70年代末發(fā)展起來的一種新型物質分離、精制技術,它是利用超臨界流體,即其溫度和壓力略超過或靠近臨界溫度和臨界壓力,介于氣體和液體之間的流體作為萃取劑,從固體或液體中萃取出來某種高沸點或熱敏性成分,以達到分離和提純的目的。
超臨界萃取過程針對不同的原料,不同的分離目標,有著不同的技術路線和工藝過程,生產性的超臨界萃取裝置一般都要單獨設計制造。萃取過程的設備主要有萃取釜和分離釜兩部分,并配有適當壓縮裝置和熱交換設備,固體原料的萃取過程可分為3種:等溫法、等壓法和吸附法。超臨界流體萃取技術多用于固體物料萃取,但實踐證明在液-液萃取分離中亦有優(yōu)勢,液體物料可呈現連續(xù)操作,提高效率,降低成本。
超臨界CO2流體兼具氣體和液體的特性,溶解能力強,傳質性能好,加之其無毒、惰性、無殘留等一系列優(yōu)點,以CO2為工作介質,實用價值較大,是目前首選的清潔型工業(yè)萃取劑,廣泛應用于食品、香料和醫(yī)藥等行業(yè),國內外應用較廣。
國外某公司萃取設備工藝流程:2個973L的萃取釜串聯,被萃取的物料裝在原料筐中被放入萃取釜,密閉釜口,系統(tǒng)抽真空,然后開啟閥門,啟動循環(huán)泵升壓,超臨界CO2流體由高壓泵加壓送到萃取釜,經過高壓過濾器后,用閥門控制流量降壓,加熱后進入一級分離釜,解析出被萃取物質,剩余未被分離的物質被流體帶出,再用閥門控制流量降壓,加熱后進入二級分離釜,解析出剩余的被萃取物質。經過低壓過濾器后,將CO2流體冷卻,用分子篩除水、再全部冷凝為液態(tài)的CO2,送入溶劑儲罐中再循環(huán)使用。
國內某公司開發(fā)的CO2超臨界萃取設備的工藝流程:液體CO2由高壓泵加壓到萃取工藝要求的壓力并傳送到換熱器,將CO2流體控制在萃取工藝所需溫度,然后進入萃取釜,在此完成萃取過程。負載溶質的CO2流體減壓進入分離釜,CO2減壓后溶解度降低使萃取物在分離釜中得以分離。分離萃取物后的CO2流體再經換熱器冷卻液化后回到儲罐中循環(huán)使用。其中溫度控制:自動控溫<±1℃;壓力控制:自動控制穩(wěn)壓、操作安全;組合形式:二萃一塔一分;材質:接觸流體的管道、容器均采用不銹鋼材料。
3 生物工業(yè)萃取設備的發(fā)展趨勢
近幾年,國內萃取設備行業(yè)發(fā)展較快,基本上形成了市場體系,但是國產設備對市場的滿足率有待提高,設備技術上和國外 水平相比尚有差距,萃取設備的發(fā)展更新速度落后于萃取技術的發(fā)展,如對極性大、分子量超過500(Dalton)的物質,需要夾帶劑或在很高的壓力下進行萃取,安全問題十分突出,且價格較昂貴。總體上,萃取設備未來發(fā)展將體現出以下一些變化。
(1)強化傳質分離形式的轉變。新技術的出現極大刺激了萃取工業(yè)的發(fā)展,傳統(tǒng)方式強化傳質分離的途徑是采用外界輸入能量以使兩相獲得很大的傳質比表面積和良好的接觸,今后強化傳質分離的手段將趨向于細化液滴尺寸和增加相際湍動,如通過超聲波、撞擊流和旋轉流等途徑來實現強化傳質分離的目的。
(2)萃取裝備與檢測技術在線聯合。如超臨界CO2流體萃取-氣相色譜聯用、超臨界CO2流體萃取-液相色譜聯用,這些聯用技術使得萃取物萃取后不用轉移即可進行直接分析,將氣相色譜與液相色譜用作檢測手段,可以充分發(fā)揮這些現代分析技術的優(yōu)點,對萃取效率、萃取物組分、有效成分含量以及萃取物純度等進行深入研究,進而進行準確的定量分析,并以直觀的色譜圖反映出來。
(3)新型萃取設備在工業(yè)上逐步得到應用。隨著技術的進步,新型萃取設備不斷產生并得到應用,如微波-萃取技術、固相微萃取技術等,但有些新設備的投資和操作費用也都較為高昂,如何研制出簡潔高效、安全經濟且適合特定技術或流程的新型萃取設備,還有待萃取裝備行業(yè)的進一步探索和發(fā)展。