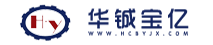
運行中應研究進離心脫水機的濃縮污泥含固率的要求范圍,進料量(裝機容量),產(chǎn)量,離心機差速、轉速,不同類型聚丙烯酰胺(PAM)加注率、投加濃度對離心機脫水后的污泥含固率、分離水SS值和回收率的影響。
若要離心脫水機的污泥脫水處理達到理想的分離效果,可以從兩方面來考慮:
(1)轉速差越大,污泥在離心機內(nèi)停留時間越短,泥餅含水率就越高,分離水含固率就可能越大。反之,轉速差越小,污泥在離心機內(nèi)停留時間越長,固液分離越徹底,但必須防止污泥堵塞。利用轉速差可以自動地進行調節(jié),以補償進料中變化的固體含量。
(2)當污泥性質已經(jīng)確定時,可以改變進料投配速率,減少投配量改善固液分離;增加絮凝劑加注率,可以加速固液分離速度,提高分離效果。
常見問題:
①開機報警或振動報警
離心脫水機開啟時低差速報警引起主電機停機或者振動較大、聲音異常,造成報警停機。上述情況為上次停機前沖洗不徹底所致,即沖洗不徹底會導致兩種情況發(fā)生:一是離心機出泥端積泥多導致再次開啟時轉鼓和螺旋輸送器之間的速差過低而報警;二是轉鼓的內(nèi)壁上存在不規(guī)則的殘留固體導致轉鼓轉動不平衡而產(chǎn)生振動報警。
②軸溫過高報警
這主要是由于潤滑脂油管堵塞致潤滑不充分、軸溫過高。由于離心脫水機的潤滑脂投加裝置為半自動裝置,相對人工投加系統(tǒng)油管細長,間隔周期長,投加1次潤滑脂容易發(fā)生油管堵塞的現(xiàn)象。一旦發(fā)生,需要人工及時清理,其主要原理是較頻繁地加油以保證細長油管的有效暢通。當然,潤滑脂亦不能加注過多,否則亦會引起軸承溫度升高。
③主機報警而停機
開啟離心脫水機或運行過程中調節(jié)脫水機轉速,主電機變頻器調節(jié)過大或過快,容易造成加(減)速過電壓現(xiàn)象,導致主電機報警。運行中發(fā)現(xiàn),一般變頻調節(jié)在2Hz左右比較安全。離心脫水機在沖洗狀態(tài)下,尤其在高速沖洗時,也易造成加(減)速過電壓現(xiàn)象,所以在高速沖洗時離心脫水機旁應有運行人員監(jiān)護。
④離心脫水機不出泥
在離心脫水機正常運轉的情況下,相關設備正常運轉,但出現(xiàn)不出泥現(xiàn)象,濾液比較混濁,差速和扭矩也較高,無異響,無振動,高速和低速沖洗時扭距左右變化不大,亦出現(xiàn)過扭距忽高忽低的現(xiàn)象,再啟動時困難,無差速。這種情況多發(fā)生在雨季,由于來水量大,對生物池的污泥負荷沖擊大,導致剩余污泥松散、污泥顆粒小。而污泥顆粒越小,比表面積越大(呈指數(shù)規(guī)律增大),則其擁有更高的水合強度和對脫水過濾更大的阻力,污泥的絮凝效果差且不易脫水。此時,如不及時進行工藝調整,則離心脫水機可能會出現(xiàn)扭矩力不從心的現(xiàn)象(過高),恒扭矩控制模式下差速會進行跟蹤。一旦差速過大,很容易導致污泥在脫水機內(nèi)停留時間短、固環(huán)層薄;另一方面,轉速差越大,由于轉鼓與螺旋之間的相對運動增大,對液環(huán)層的擾動程度必然增大,固環(huán)層內(nèi)部分被分離出來的污泥會重新返至液環(huán)層,并有可能隨分離液流失。這種情況下會產(chǎn)生脫水機不出泥的現(xiàn)象。
在進泥濃度較低且污泥松散的情況下,采用高轉速、低差速和低進泥量運行能夠有效解決不出泥的問題,并且運行效果也不錯。高轉速是為了增加分離因數(shù),一般來說污泥顆粒越小密度越低,需要的分離因數(shù)較高,反之需要較低的分離因數(shù);采用低差速可以延長污泥在脫水機內(nèi)停留時間,污泥絮凝效果增強的同時在轉鼓內(nèi)接受離心分離的時間將延長,同時由于轉鼓和螺旋之間的相對運行減少,對液環(huán)層的擾動也減輕,因此固體回收率和泥餅含固率均將提高;低進泥量亦增加固體回收率和泥餅含固率。